
However, currently, the only operational floating wind farm of scale is Hywind Scotland, developed by Equinor and commissioned in October 2017. Globally, there are 13 announced floating offshore wind projects (nine in Europe – UK, Portugal and France, three in Asia – Japan and Korea and one in the US). Among the high potential markets, Japan has set a target of 4 GW to be installed by 2030, followed by around 2 GW in France, US and UK, and 1 GW in Taiwan. This technology involves an offshore wind turbine mounted on a floating structure, that allows the turbine to generate electricity in water depths where bottom-mounted structures are not feasible.Īccording to industry estimates, the technical potential for floating wind power is around 7,000 GW for Europe, the US and Japan combined. Structural dynamics is critical to platform design due to the dynamic excitation of the tower and the corresponding loading of the substructure primary members.Floating offshore wind is a fast evolving technology with the potential for less foundation material, shortened installation cycle and decommissioning, and additional wind power generation at water depths exceeding 50 metres to 60 metres. The platform structural design is conducted using applicable offshore codes from several classification societies, as well as extensive finite-element analysis. Reliability considerations are discussed to assess the level of redundancy required in the mooring system, in particular with regards to the one-line damaged condition. The hydrodynamic response is also validated with scale model tests.Ī four-point mooring configuration is adopted. Time-domain coupled analysis of the platform and its mooring system are performed. Rules for the design of Mobile Offshore Drilling Units are followed to verify platform stability in intact condition, and to ensure that compartmentation is sufficient to withstand damaged conditions with any compartment flooded. Development of a coupled hydro-servo-aero-elastic model constitutes a key element of the qualification process. Additional factors, such as tower dynamics and turbine controls must also be taken into account. The return period of extreme events is adjusted based on experience acquired by the wind industry.īecause of the considerable aerodynamic loads generated by the wind turbine and their effects on platform motion, the ability to solve the combined aerodynamic and hydrodynamic problem is necessary.

Selected design codes and industry standards are applied. The design process is based on a combination of advanced numerical analysis and scale model experimentation.
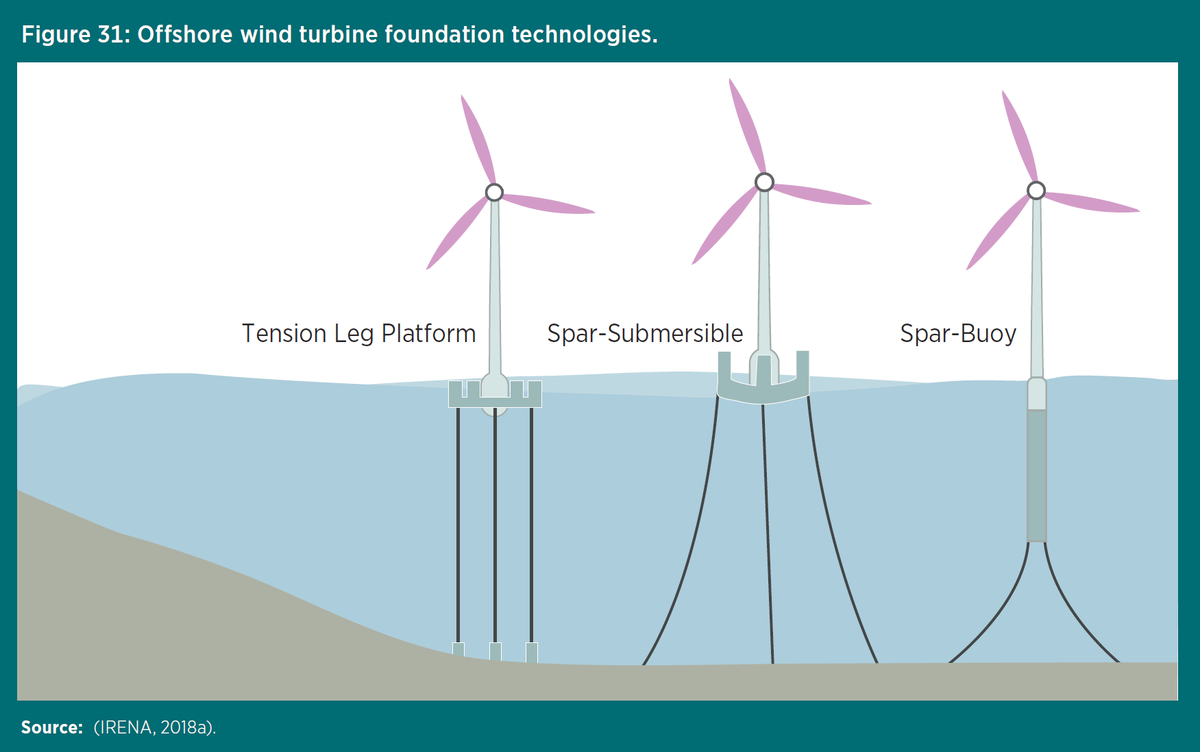
A rational and comprehensive process was followed to optimize the system while maintaining the robustness required to survive in the offshore environment. The qualification process followed for the development of a 150MW wind farm offshore Portugal is discussed.īecause of economic constraints, optimization of the platform is essential to achieve project financial targets. The platform is designed to support commercially available multi-megawatt wind turbines with no hardware modification to the turbine. The wind turbine and tower are fitted on one of the columns. The WindFloat platform is a semi-submersible platform with three columns fitted with a large horizontal water-entrapment plate at the base.

Floating foundations offer greater flexibility in term of site selection for wind farms, and if properly designed, may result in comparable availability with equivalent offshore turbines on fixed foundations, while reducing the complexity and risks associated with offshore installation.

Recent trends in the wind industry point to the use of increasingly larger and more powerful machines with rated power ranging from 5 to 10MW exclusively designed for offshore use.
